定制吹塑制品是根据客户的特定需求和要求,通过吹塑工艺生产出具有特定形状、尺寸、功能和外观的塑料制品。
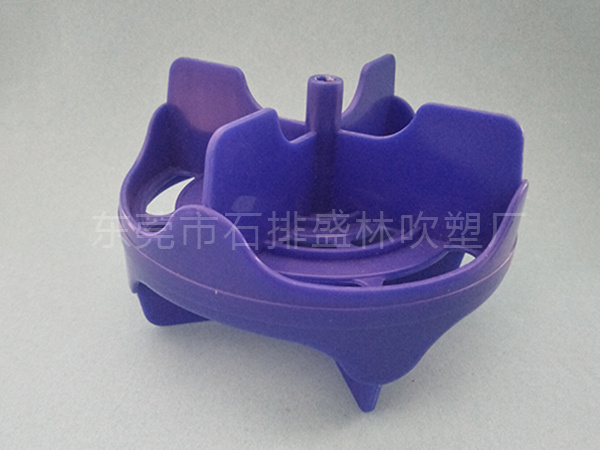
下面主要来看看定制流程分别有哪些?
需求沟通:客户与制造商沟通定制吹塑制品的具体要求,包括产品的用途、形状、尺寸、容量、颜色、功能特性等,同时提供相关的设计图纸或样品。
设计开发:制造商根据客户需求进行产品设计和模具设计。利用计算机辅助设计(CAD)软件绘制产品的三维模型,进行结构设计和优化,确保产品在满足功能要求的同时,便于吹塑成型。然后根据产品设计生成模具设计图纸,确定模具的分型面、浇口位置、冷却系统等关键参数。
模具制造:按照模具设计图纸,采用专业的模具加工设备和工艺制造模具。通常使用钢材作为模具材料,经过切削、电火花加工、热处理等多道工序,制造出高精度、高硬度的吹塑模具。模具制造完成后,需要进行试模和调试,对模具进行优化和改进,确保模具能够稳定生产出符合质量要求的产品。
材料选择:根据产品的使用要求和性能特点,选择合适的塑料原料。常见的吹塑用塑料有聚乙烯(PE)、聚丙烯(PP)、聚氯乙烯(PVC)、聚酯(PET)等。不同的塑料具有不同的物理性能、化学稳定性、透明度和加工性能,制造商需综合考虑各种因素,为客户推荐最合适的材料。
吹塑生产:将选定的塑料原料加入到吹塑机的料筒中,通过加热使其熔化并挤出成管状型坯。然后将型坯放入模具中,合模后向型坯内通入压缩空气,使型坯膨胀并紧贴模具内壁,经过冷却定型后,打开模具取出吹塑制品。在生产过程中,需要严格控制工艺参数,如温度、压力、吹胀比、冷却时间等,以确保产品的质量和一致性。
后处理:吹塑制品脱模后,可能需要进行一些后处理工序,如修边、去毛刺、印刷、贴标、装配等。修边是去除产品边缘的飞边和毛刺,使产品外观更加整洁;印刷和贴标则是为产品添加标识、图案、文字等信息,提升产品的市场竞争力;装配工序用于将多个部件组装成一个完整的产品。
质量检验:对定制的吹塑制品进行全面的质量检验,包括外观检查(如是否有气泡、裂纹、变形等)、尺寸精度测量、物理性能测试(如强度、韧性、密封性等),确保产品符合客户的要求和相关标准。对于不合格产品,及时进行返工或报废处理。
包装交付:将检验合格的吹塑制品进行包装,根据客户的要求选择合适的包装方式,如纸箱包装、托盘包装等,然后安排运输交付给客户。